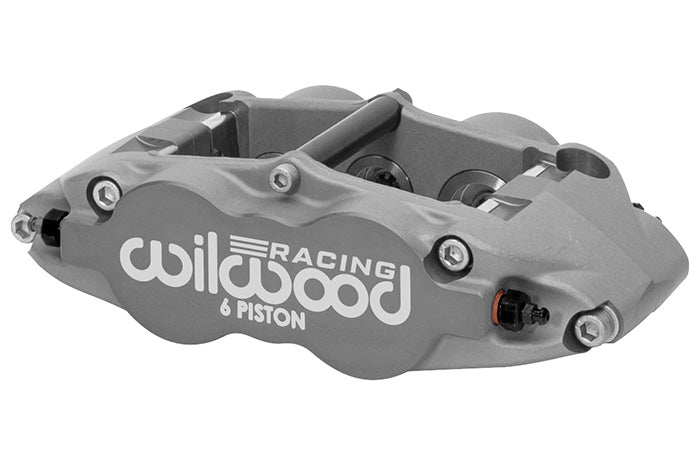
The PdV-01 wheel is done! Kind of. I'm being lazy because I know manufacturing these wheels can not happen before both the brakes and coilovers. Lets recap and cross out what is done and highlight my current priorities...
- Objective 1 - Develop the perfect wheel design (IMO) for my personal car, an Estoril Blue BMW F30
- Key Result 1 - Square setup, 18x9 ET30, 3-piece, forged rim and wheel center, custom color combo incorporating some version of a dark bronze
- Design basically done but I want to redesign to hide the hardware. Also need to remodel it to fit 19" wheels.
- KR2 - Achieve SAE J2530 certification (USA version of JWL VIA)
- Everything is lined up with the testing facility.
- KR3 -
Create an FEA model that accurately represents tire loads and replicates SAE tests - All SAE related FEA is done. Adding a little more to look at extreme braking and understanding wheel stiffness a little better.
- KR4 - Run my first laps ever on a road course on my own wheels.
- Objective 2 - Parlay Objective 1 success into a new product line.
- KR1 - Address supply chain issues for one off designs.
- Still working through a few important issues such as finding someone with a vibratory polishing machine that is designed for wheels. No existing wheel mfgs. want to do it for me as a service.
- KR2 - Align designs and pricing with the PdV brand.
- KR3 - Expand PdV product line with opportunities that are presented in the wheel development process.
- This effort has helped kick off a badass brake kit and maybe drop spindles now that I have the knuckles CMM'd
- KR4 - Expand O1 wheel design to fit 19" and 20" wheels
- Still to do but I'm abandoning 20's because no one really races 20's and that's where I want to take the brand.
- KR5 - Develop 2nd design, a unique 5-spoke.
- Objective 3 - Copy Obj. 1 & 2 for custom coilovers
- KR1 -
Source cheap rebuildable coilovers, preferably buying only parts instead of full assemblies - Done. A BC Racing kit is in-house and ready for some dyno work.
- KR2 - Replace hydraulic components that are critical for performance with my own design. Benchmark key performance attributes.
- Some designs are done but may start with Ohlins/Bilstein guts or possibly adapt Penske regressive bits to go way nuts before making bespoke pistons.
- KR3 - Develop business plan with two options. 1) Rebuild service for new or used kits with PdV components 2) Sell new complete coilover kits already built with PdV components.
- I think selling just the sealed and tuned cartridge for existing BC customers to swap would be a killer deal...
OK, so the critical wheel FEA step is complete. According to industry standard I'm taking my wheel design well above and beyond what any other wheel designer would do except for suppliers of professional racing cars, which I'm on par with and ultimately is the quality/strength level I want to target for the business.
Cheap rebuildable coilovers. Done. BC Racing is perfect so far. I'm currently seeking out local shops with a shock dyno to help with all the tuning I'll be doing so I don't have to buy a dyno.
On to the good stuff. I have been hyper-focused on the F30 front brake kit so in this post I'll cover a couple things.
1) What are my performance targets given a roughly $2,000 retail price target?
Unbeknownst to some (dare I say many), a race car does not stop faster with 8ft rotors and 34 piston calipers. For the Volvo S60R and BMW F30, Brembo 4 piston calipers and big rotors are standard with exception for some BMW models. Sticking to the readily available 345 to 380mm rotor options seems reasonable. So what do I really want to achieve?
- Low cost initial parts as well as replacement parts over time compared to what's available.
- Improved stiffness. This will be hard to quantify compared to the Brembos without CAD but is really inherent in the design due to geometry and other features in the design required to mount a caliper radially. Many miles of testing will prove pad wear is even and long lasting compared to OE Brembos. I've seen back to back results on other platforms with Wilwood radial mounted calipers that already prove it to me.
- Full floating rotors are a hard requirement because racecar.
- Add lightness. I haven't verified the weight of the stock calipers yet but I estimate the 6.9lb Wilwood caliper with pads will save around 7lbs per corner. Perhaps another 2-4lbs for each floating rotor.
- Improved thermal capacity should be inherent given the thicker rotor rings. Perhaps the aluminum hats will extend wheel bearing life for the hardcore racers.
- Optional improved pedal feel. If someone tells you they prefer to modulate their brakes with longer pedal travel, well... I was told I shouldn't say anything if I don't have anything nice to say. I only say optional for now because I'm maintaining roughly the same piston area as stock as I develop the front first which needs to work with the stock rear calipers. A simple part number change and the same Wilwood calipers with a 15% smaller piston area will noticeably quicken engagement and stiffen the pedal feel.
- Racing pedigree. Sure stock might be from Brembo but that doesn't mean much. This kit will allow for various pad compounds, various piston designs for thermal management, forged not cast calipers, various rotor ring options, probably better airflow through the two piece rotor, and even easier maintenance.
2) How do I design my own floating rotors without making custom floating rotor hardware?
The intent was always to use Wilwood calipers but not Wilwood rotors. I didn't know about their lug drive system at the time. Sourcing the bobbins or whatever system you want to use, was a surprising task at first. I am confident I just didn't find the right source online to sell me copious amounts of floating rotor hardware. People need replacements right?
Well I'm glad cause when I dug deeper into the Wilwood catalog I discovered the lug drive system which is, to be honest, fucking awesome. Zero bolts required, no safety wire needed, and no expensive bobbins or other hardware. For $20 a rotor you get a big ass retaining ring and some steel inserts.
Young engineers, perk up! How do I design my rotor hat to work with their floating hardware when I know tight tolerances are involved? I bought one of their rotor hats that had 12 "lugs" and took very accurate measurements of all 12 lug features. Pretty simple and I'm highly confident after considering the average, max, min, median, and standard deviation I'll nail the fit on the first try even if it means my tolerances are a little tighter than whatever Wilwood has on their drawings.
Rotors done. For now, my rotors are aligned with the stock rotor centerline but I am considering moving it away from the wheel as much as possible to improve caliper clearance.
3) What loads and safety factors do I design for?
This is the important bit and required some research to be safe. My customer's lives are in my hands after all! Safety is of course the under-appreciated aspect of engineering I hear about from other engineers seeking fame/fortune/gratitude. ;)
So I read some books and research papers with sweet titles like "Brake Design and Safety", "Braking for Road Vehicles", and one particularly interesting one called "FEA Analysis and Correlation of Thermo-Mechanical Deformations of a Disc Brake Rotor".
Side note for engineers, read that last paper and make sense of the section with figures 12-15. I verified it with my own FEA but unfortunately can't package the lug drive rotor to mount on the inboard rotor face without moving the caliper closer to the wheel and there is no room for that. The benefit of not extending the rotor hat of course is the reduced cost of hogging out a smaller billet of aluminum.
To summarize, a vehicle's stopping power is obviously based on tire performance and there is a force balance between the tire and the brake pad, the pedal and the calipers, as well as between the front and rear systems that needs to be considered. So now I have that Matlab script. Fun stuff!
At this point I can say I have some system requirements and those need to drive component requirements. An important one would be how much torque is applied to the caliper bracket based on the pad pressure/friction requirement and the moment created by the offset of the rotor centerline to the caliper's radial mounting bolts? Then go a level deeper to find that the stiffness of the caliper and the radial bolt pretension is so important to the bracket itself, you can't easily and accurately analyze just the bracket in a component level FEA in Solidworks. That isn't a terrible thing, I want to verify and instruct on assembly bolt torques that are safe and can be verified in an assembly level FEA.
I hope by now it is abundantly clear that I'm trying to discuss the engineering process as much or more so then what I'm designing, why, and how many cool colors it can come in. If you are enjoying this please comment and let me know.
Below is a list of rotor and caliper combinations to help sort out my options and ensure I can set and meet certain design targets. If you compare the M sport and M performance data you'll notice some variation in the calculated bias and ratios on what is for all intents and purposes an identical car. Take that variation and then assess how Stoptech modified the system for their kits and you start to see what can change and by how much to maintain a properly functioning brake system.
So now I have 3 Wilwood options to move forward with and ultimately every customer will as well. Base and M sport guys can save some money by going with FNSL6R calipers. They just have to decide if they want to maintain the stock pedal characteristics or move toward something that might improve pressure modulation and make heel/toe maneuvers a little easier.
The issue with the two other FNLS6R options with 381mm rotors is, the FNSL6R caliper is not supposed to be used with rotors larger than 355mm. I'm still looking into this but assuming that's true then a different, more expensive caliper is required called the Aero4. The Aero4 is a serious caliper yet can still come with piston dust seals if you wanted. The Aero4 combo would increase torque a lot and reduce piston area, perhaps too much. Some testing is required but its potentially a killer racing package for less then $2500.
In terms of caliper bracket design, I think I'm good to go on the FNSL6R version. Stress levels are low at unrealistically high max torque, like under 120MPa low for 6061-T6 which is perfect.
For the nerds that might be reading this, my sim setup was an assembly (most parts hidden in pics) with a dummy steel (for stiffness) caliper, the bracket with steel spacers, and dummy knuckle mounts that were fixed in space. Preloaded bolts were used with global contact, no penetration, and 0.2 friction coefficient.
Bolts were used but the final design will have studs which makes caliper installation a bit easier and I think makes for a more professional look.
I've rambled on long enough. I do want to end with one bling bling progress pic. Almost all of my current F30 projects are fully detailed and assembled in CAD now.